Torque Angle Method
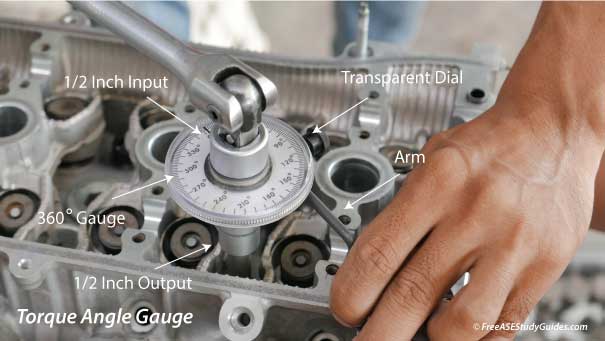
Manufacturers of modern engines recommend torquing the bolt with a torque wrench and then turning a certain number of degrees. Torque-to-yield bolts are typically torqued to snug with a torque gauge and then angled. This process is known as the torque angle fastening method.
Much of the turning effort turning the torque gauge is spent overcoming friction. In addition, variables like dirt and different lubricants affect the torque reading. Torquing a bolt to a snug fit with a torque wrench and then turning the bolt an exact number of degrees eliminates these problems and is more accurate and consistent.
Manufacturers have used torque to yield bolts to fasten cylinder heads to engine blocks for years. As a result, specifications typically require a torque angle setting.
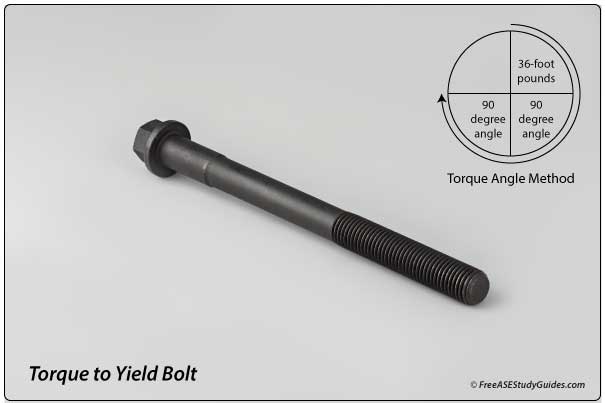
For Example:
Torque the cylinder head bolts from the inside out, starting at the intake manifold to 36-foot pounds, and then apply two angled turns.
- This first pass snugs the bolt without stretching it.
- The second pass is a 90-degree angle or a quarter turn.
- The third pass is another 90-degree angle.
Most cylinder heads are aluminum; head gaskets are MLS or multi-layered steel and fastened to iron or aluminum engine blocks. Iron and aluminum expand at different rates resulting in movement between the dissimilar metals. For example, when heated, aluminum expands over twice the rate of iron.
The torque to yield bolt can adapt to the expansion of the aluminum cylinder head, applying a more constant clamping force. As a result, they are popular in modern vehicles.
Many manufacturers require torque angle settings on the crankshaft and connecting rod cap bolts. As a result, the manufacturer may require new bolts. Torque to yield bolts can stretch into plastic deformation and will not provide enough clamping force for the cap.